In a previous post, we discussed the broad differences between anodic and cathodic forms of environmentally assisted cracking (EAC). In that article, we concluded that while localized corrosion appears to be a prerequisite for anodic EAC modes such as stress corrosion cracking (SCC), hydrogen-assisted EAC mechanisms like hydrogen stress cracking (HSC) are exacerbated at cathodic potentials. We also stated that sulfide stress cracking (SSC) was a form of HSC in the presence of H2S [1]–[2]. But, is it really?
Effect of applied potential
In 1978, Dunlop published a comprehensive investigation on the EAC of low strength nickel low alloy steels (LAS) (ASTM A203 Grade B and E) in 0.5 wt% acetic acid solutions saturated with H2S, as well as low partial pressures of H2S, \({p_{H_{2}S}}\).[3] The steels were normalized for 1h at 815–843°C. The actual yield strength of the LAS Grade B and E was 398 MPa (57.7 ksi) and 359 MPa (52.1 ksi), respectively. The authors found that while cracking was exacerbated at anodic potentials, a cathodic polarization retarded or eliminated crack growth. Dunlop, thus, concluded that the EAC mechanism was a form of SCC, i.e., initiated anodically, rather than SSC. Dunlop named this type of EAC sulfide corrosion stress cracking (SCSC), which is now an obsolete term.
As seen in Figure 1, cracking was observed only on the tension side of U-bend samples. In all cases, elongated pits about 200 μm deep were present. Furthermore, because cracking occurred on low strength steels at very low \({p_{H_{2}S}}\) (i.e., 0.001 atm), Dunlop remarked that SCSC could not be related to hydrogen embrittlement. In his view, hydrogen stress cracking was only associated with higher strength steels. According to Dunlop, because SCSC required selective anodic dissolution, SCSC could be controlled using corrosion inhibitors that would prevent localized corrosion, such is the case in environments containing nitrate, caustic, carbonate, CO/CO2, and phosphate.
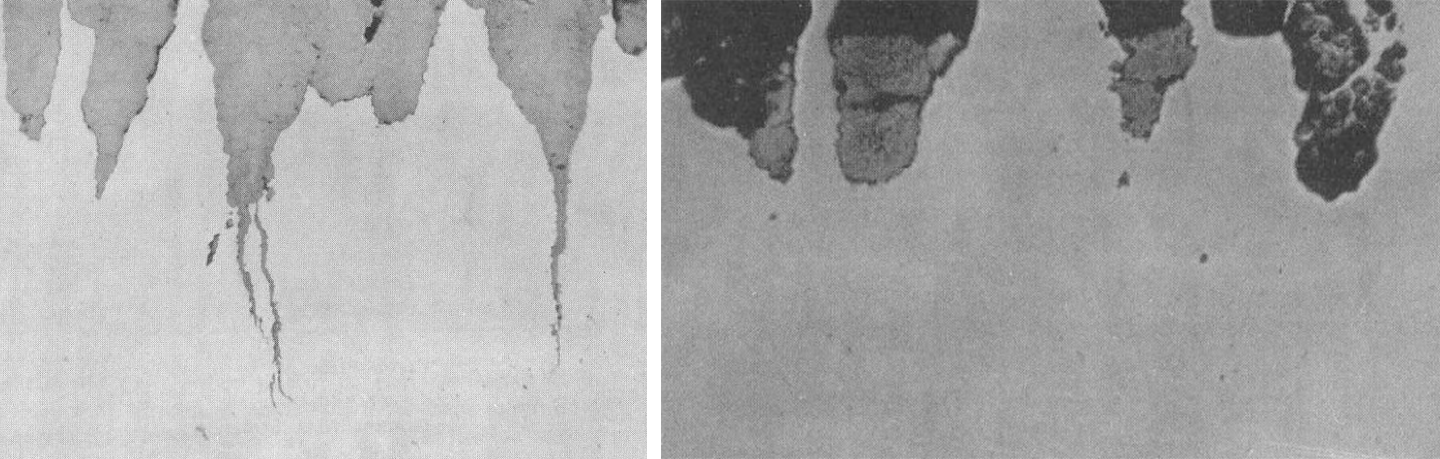
Dunlop’s work caused much controversy at the time, which we covered in our recent review paper.[4] The debate primarily focused on experimental details such as the speciation of H2S at the pH used by Dunlop or the severity of the 3-point bent beam tests (i.e., the so-called Shell test). However, no mention was made to the fact that hydrogen evolution can still take place at EOC or even at anodic potentials if the potential at the bottom of the pit is below the reversible potential of the hydrogen evolution reaction, which is the case in most sour service environments. Additionally, the effect of microstructure was not addressed.
In 1986, Yoshino and Minozaki published a comprehensive investigation on the EAC of 1% Cr–0.5% Mo LAS with variable nickel content.[5] Independently of the fact that the authors showed that nickel additions up to 2 wt% had no effect on the EAC resistance of LAS, Yoshino and Minozaki demonstrated that sulfide stress cracking is, indeed, a form of hydrogen stress cracking. Experiments conducted at various potentials, from cathodic to anodic, showed that the elongation to failure decrease with decreasing potential, coinciding with an increase in the hydrogen permeation current density, Figure 2.
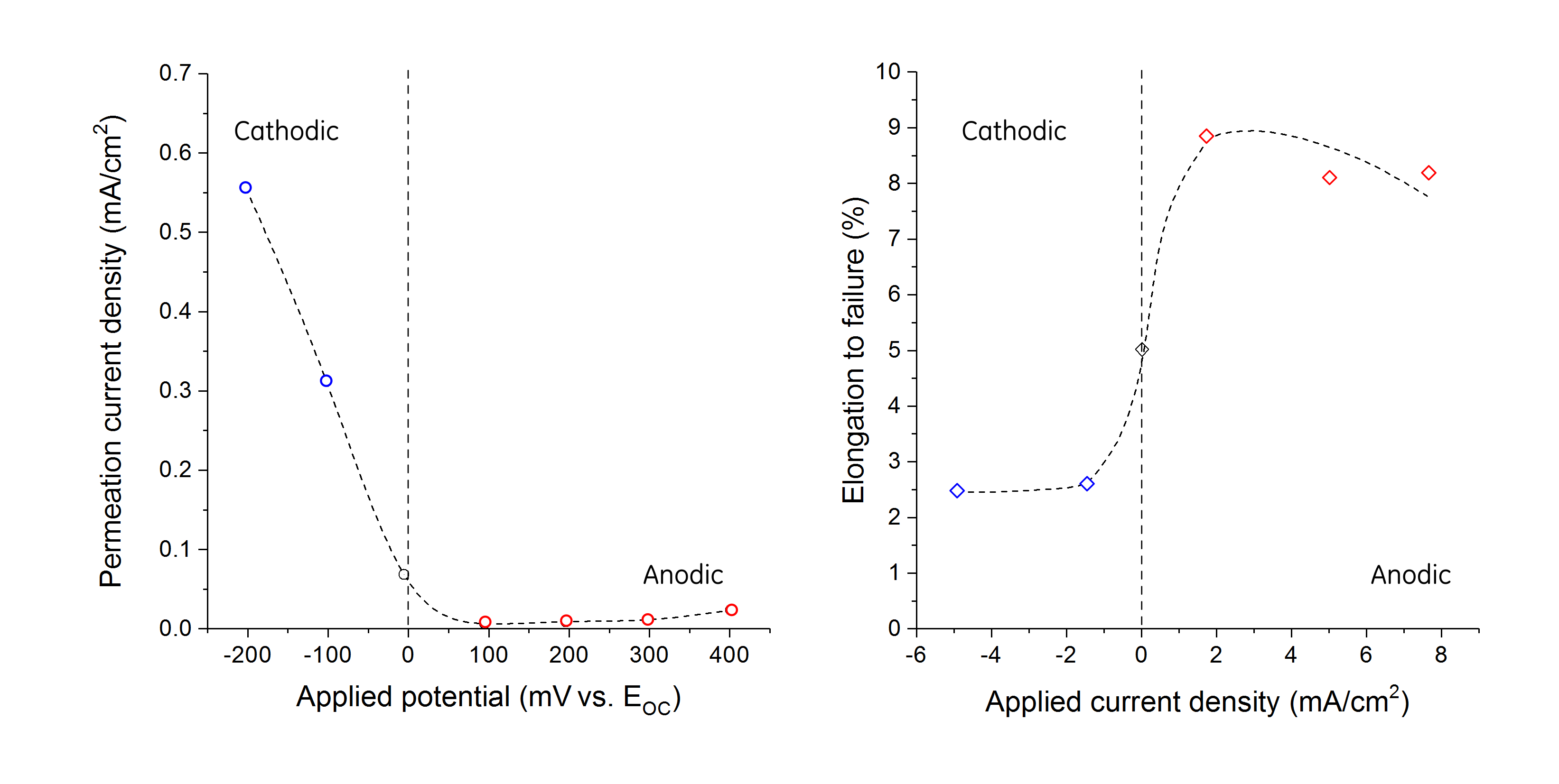
Interestingly, at cathodic potentials cracking occurred with no localized corrosion. Pitting corrosion was, however, a prerequisite for crack propagation at EOC and under net anodic polarization as shown in Figure 3. The depth of the pits before crack propagation varied between 200 and 300 μm.
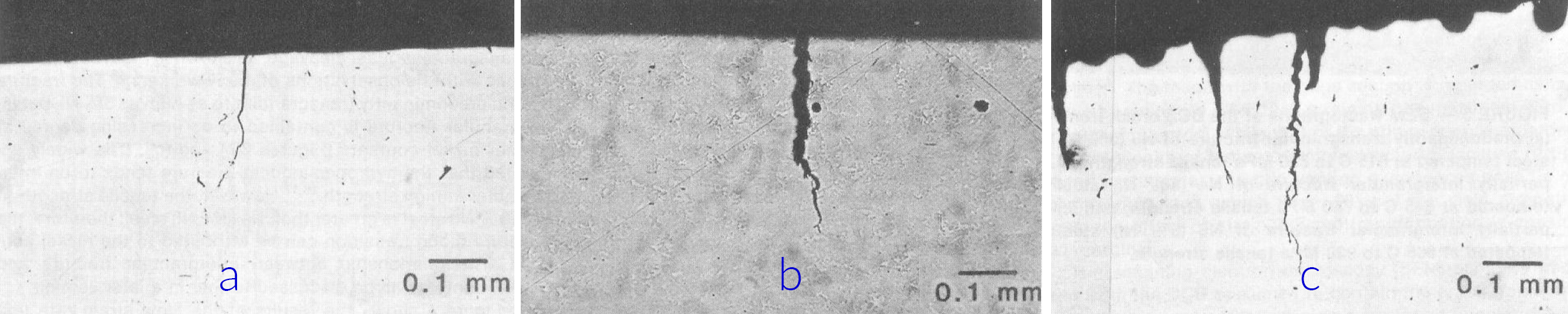
What happens at the open circuit potential?
Although tests conducted at different applied potentials can provide insights into EAC mechanisms, the most relevant situation in service involves exposure at EOC. In their 1986 publication, Yamane postulated an elegant mechanism to explain SSC of low alloy steels. [6] According to Yamane, pitting corrosion controls SSC initiation. In his model, pitting corrosion was referred to as the Active Path Corrosion (APC). Hydrogen embrittlement, in contrast, controls crack propagation, Figure 4.
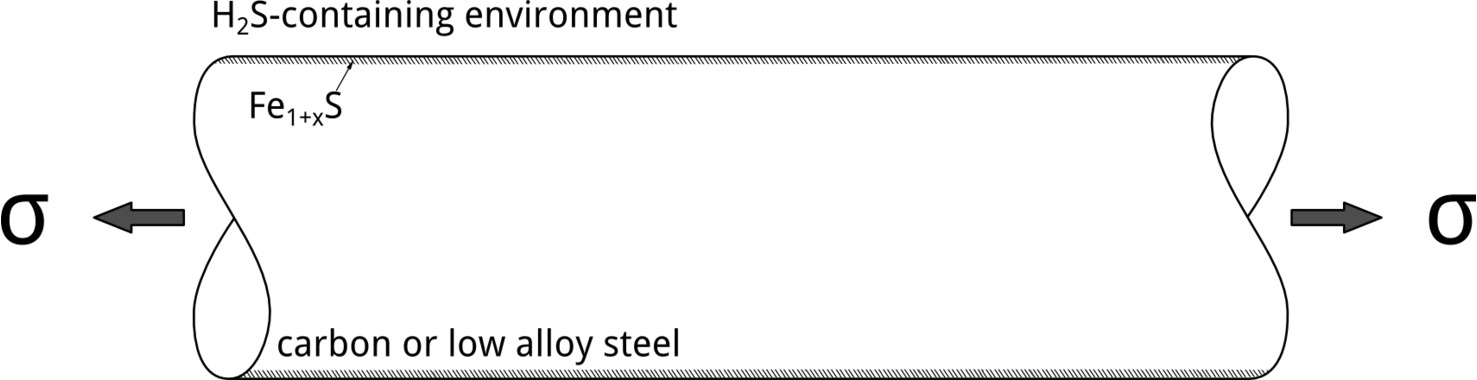
It is possible to explain Yamane’s model by looking at how the potential drops along the APC region. In Figure 5, the formation of an iron sulfide film at the surface is a prerequisite for localized corrosion initiation.[7] The Fe1+xS film leads to the localization of the attack, which can happen when EOC is above the pitting potential, EP. As the potential drops along the pit due to Ohmic effects, hydrogen evolution can occur at the bottom, which could, then, lead to SSC crack propagation due to stress concentration and readily available hydrogen. H2S facilitates hydrogen absorption, increasing the dissolved hydrogen content, by acting as hydrogen recombination poison.
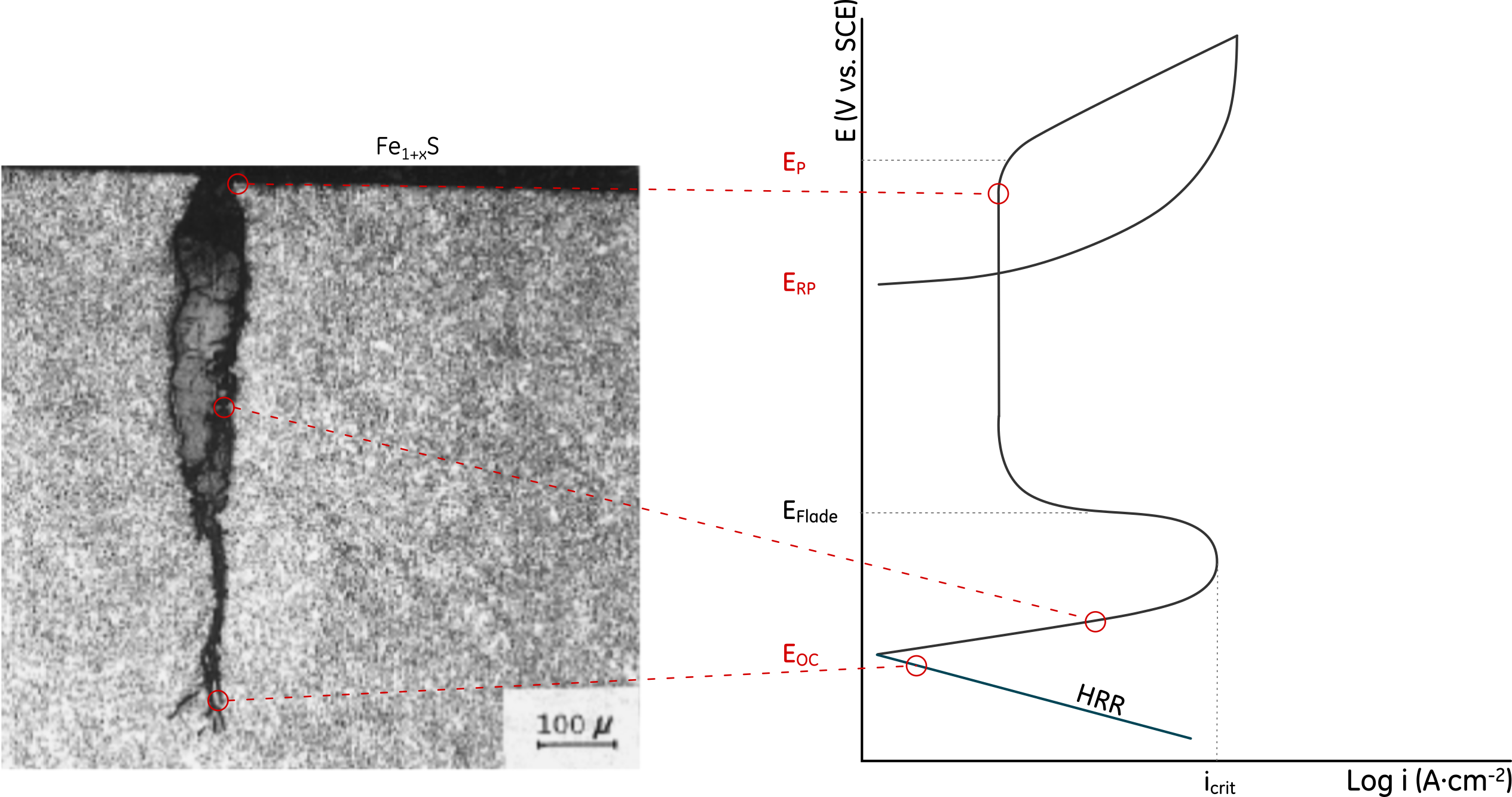
Conclusions
So, what does it all mean?
- Although it is now well accepted that SSC is, indeed, a form of HSC, it is not entirely clear what happens at the open circuit potential. In this regard, the model proposed by Yamane appears as a reasonable explanation (at least to me).
- Since the APC concept requires the formation of a protective scale on the surface, the resistance to SSC at EOC should be controlled by the stability of the passive film or scale, as proposed by Dunlop.
- Thus, can we control SSC by the formation of, for example, robust iron carbonate scales prior to the exposure to a H2S-bearing environment?
References
- ↩ “Types of Cracking in Wet H2S-Containing Environments”, in European Federation of Corrosion Publications Number 16: Guidelines on Materials Requirements for Carbon and Low Alloy Steels for H2S Containing Environments in Oil and Gas Production, (Eliassen, S. & Smith, L., 3rd Ed., Maney Publishing, Leeds, UK, 2009): p. 12–14.
- ↩ ASTM NACE/ASTMG193–12d, “Standard Terminology and Acronyms Relating to Corrosion”, ASTM International, West Conshohocken, PA, 2012.
- 10.5006/0010–9312–34.3.88 (1978). ↩ Dunlop, A. K. “Stress Corrosion Cracking of Low Strength, Low Alloy Nickel Steels in Sulfide Environments.” Corrosion 34, 88–96, doi:
- 10.1515/corrrev–2014–0027 (2014). ↩ Kappes, M., Iannuzzi, M., Rebak, R. B. & Carranza, R. M. “Sulfide stress cracking of nickel-containing low-alloy steels.” Corros. Rev. 32, 101–128, doi:
- 10.5006/1.3586000 (1986). ↩ Yoshino, Y. & Minozaki, Y. “Sulfide stress cracking resistance of low-alloy nickel steels.” Corrosion 42, 222–233, doi:
- ↩ Yamane, Y., “Effect of Ni on sulfide stress corrosion cracking in low alloy steels,” CORROSION/86, paper no. 167 (Houston, TX: NACE International, March 17–21, 1986).
- 10.5006/1.3299824 (1992). ↩ Craig, B., Brownlee, J. & Bruno, T. “Sulfide stress cracking of nickel steels.” Corrosion 48, 90–97, doi: