Introduction
In a previous post, we discussed a fracture mechanics (FM) based approach that could be used to demarcate a critical size, \(a_{Crit}\), above which a sharp trench or an elongated pit could lead to fast brittle environmentally assisted cracking (EAC). Discussions I have read since then in different online forums all seem to assume that pits are a prerequisite for environmental cracking. But, are they? Is EAC possible without localized corrosion?
In this post we will explore the different forms of EAC that could affect carbon and low alloy steels (LAS) as well as Corrosion Resistant Alloys (CRA) in oil and gas production environments.
Environmentally assisted cracking regions.
EAC, which is defined by ASTM G193 as cracking of a material wherein, an interaction with its environment is a causative factor in conjunction with tensile stress [1], can occur in two different electrochemical potential regions. In this regard, both cathodic and anodic potentials can lead to various forms of environmental cracking.
Figure 1 is a schematic representation of the cathodic and anodic response of a material that is either spontaneously passive or develops a surface protective film in the given environment. In Figure 1, \(E_{OC}\) is the open circuit potential, \(E_P\) the pitting potential, \(E_{RP}\) the repassivation potential, and \(E_{CP}\) the typical potential achieved by sacrificial AlZnIn anodes.
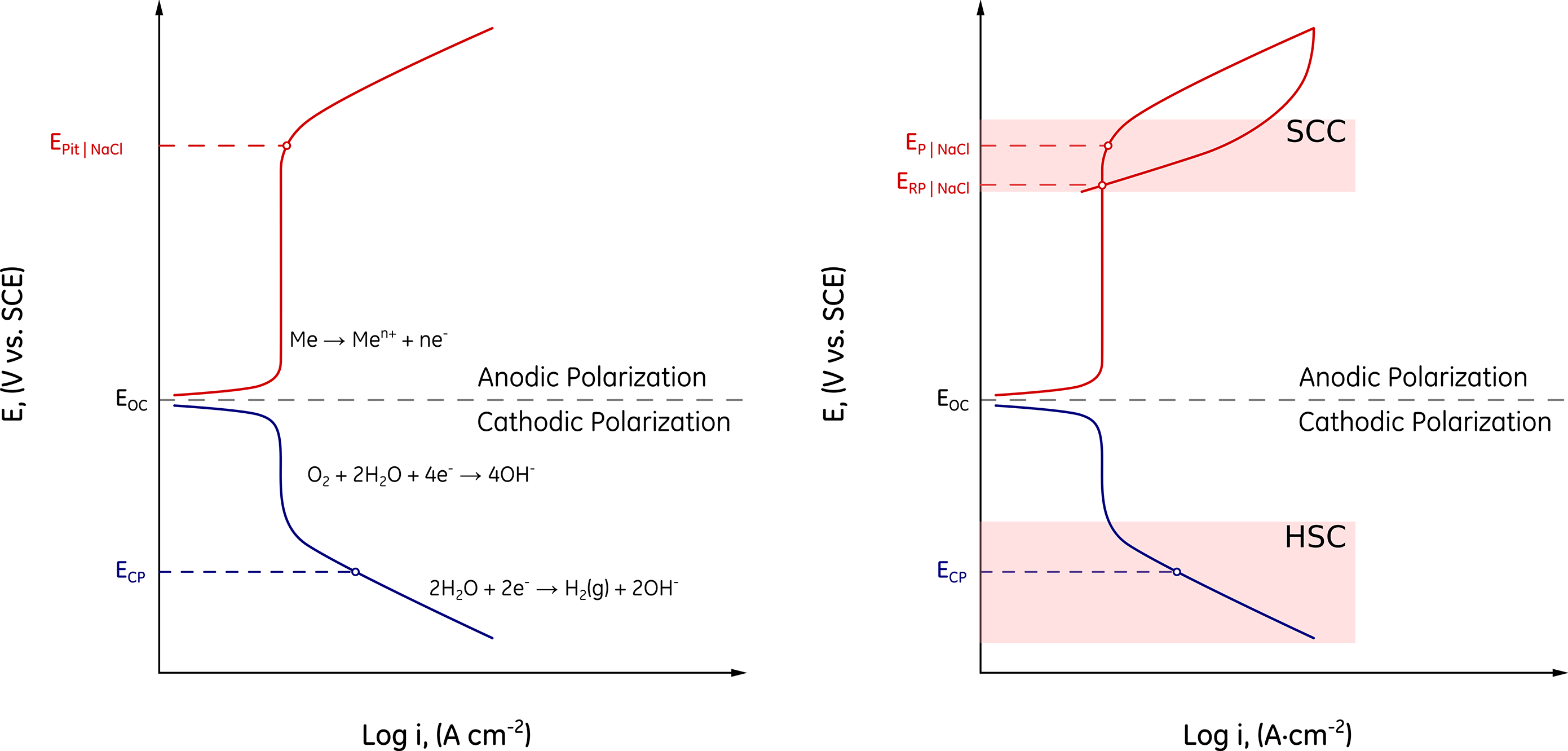
In this particular example, the environment is aerated as can be inferred by the diffusion-limited region in the cathodic portion of the curve. Hydrogen evolution takes place below the reversible potential of the hydrogen REDOX reaction, \(E_{REV}^{{H^ + }/H}\). Hydrogen evolution becomes dominant at more negative potentials, where the current of the hydrogen reduction reaction (HRR) surpasses the limiting current of the oxygen reduction reaction (ORR), \(i_{lim}\).
The anodic polarization branch is first characterized by a low passive current density \(i_{Pass}\). The passive or protective film grows in this region as the polarization, i.e. the difference between the applied potential, \(E_{App}\) and the \(E_{OC}\), increases. Stable pitting corrosion takes place above \(E_P\). Pits cease to grow below \(E_{RP}\) upon scan reversal.
Hydrogen stress cracking (HSC), defined as the cracking of a metal under the combined action of tensile stress and corrosion in the presence of water and nascent H [1], is exacerbated by applied cathodic potentials, Figure 1 (right). In this regard, SSC is a particular form of HSC in the presence of hydrogen sulfide, \(H_2S\) [2]. Therefore, HSC and SSC become more severe at applied potentials below \(E_{OC}\) [3].
In contrast to HSC and SSC, stress corrosion cracking (SCC), defined as the cracking of a material produced by the combined action of corrosion and sustained tensile stress (residual or applied) [1], is an anodic process that takes place in a region where the passive film becomes unstable. Thus, SCC of LAS and CRA typically occurs in a potential region between \(E_{RP}\) and \(E_P\), Figure 1 (right). In other words, whereas localized corrosion is a prerequisite for SCC [4]–[5], HSC and SSC can occur at cathodic potentials in the absence of localized corrosion.
Because conditions that promote pitting corrosion can also lead to SCC, high temperatures, high chloride concentrations (or anions of strong acids such as \(Br^-\) and \(F^-\)), higher \(P_{H_2S}\) and \(P_{CO_2}\), the presence of elemental sulfur, \(S^0\), and lower pH values all increase SCC susceptibility [4]–[5]. But, if pits are not a prerequisite for HSC or SSC, where do cracks originate?
Atomic or nascent hydrogen is generated when components are polarized cathodically below \(E_{REV}^{{H^ + }/H}\). In practice, both galvanic coupling to a less corrosion resistant material and cathodic protection can lead to hydrogen evolution [6]–[7]–[8]–[9]. Hydrogen that recombines to form \(H_2(g)\) does not represent a threat [6]–[9]. However, H atoms that diffuse into the metal can lead to HSC [9]. Areas of high stress such as threads in threaded connections or sharp corners that can act as notches attract H atoms and contribute to fast brittle failure [4],[9]. Cracking due to HSC often occurs at applied stress levels far below the yield strength of the material [8]. Arguably, the fact that no localized corrosion is needed for HSC to occur combined with the complete brittle nature of the failure makes HSC and SSC more dangerous than SCC.
Figure 2 [10] illustrates the difference between EAC of a 5 wt% Ni containing LAS exposed to \(H_2S\)-saturated NACE TM–0177 Solution A (5% NaCl and 0.5% glacial acetic acid, pH= 2.6–2.8) [11] at room temperature. The image on the left shows SSC secondary cracking that initiated at cathodic potentials as the result of a –1.5 mA.cm–2 applied current density. The micrograph on the right shows cracking on the same material originating from an anodic polarization as a result of a +1.8 mA.cm–2 applied current density. As seen in Figure 2, at net cathodic potentials cracking initiated at the regions of high stress concentration with no localized corrosion. In contrast, pitting corrosion was clearly visible after exposure to anodic potentials. All cracks started from pit bottoms. We will discuss SSC mechanisms in more detail later on, but pitting of carbon and low alloy steels in \(H_2S\) environments is a consequence of the formation of protective iron sulfide scales [12]–[13]. Yamane et al. referred to elongated pits or trenches as Active Path Corrosion (APC) in their proposed SSC mechanism [3]. We will discuss Yamane et al. in the next blog post.
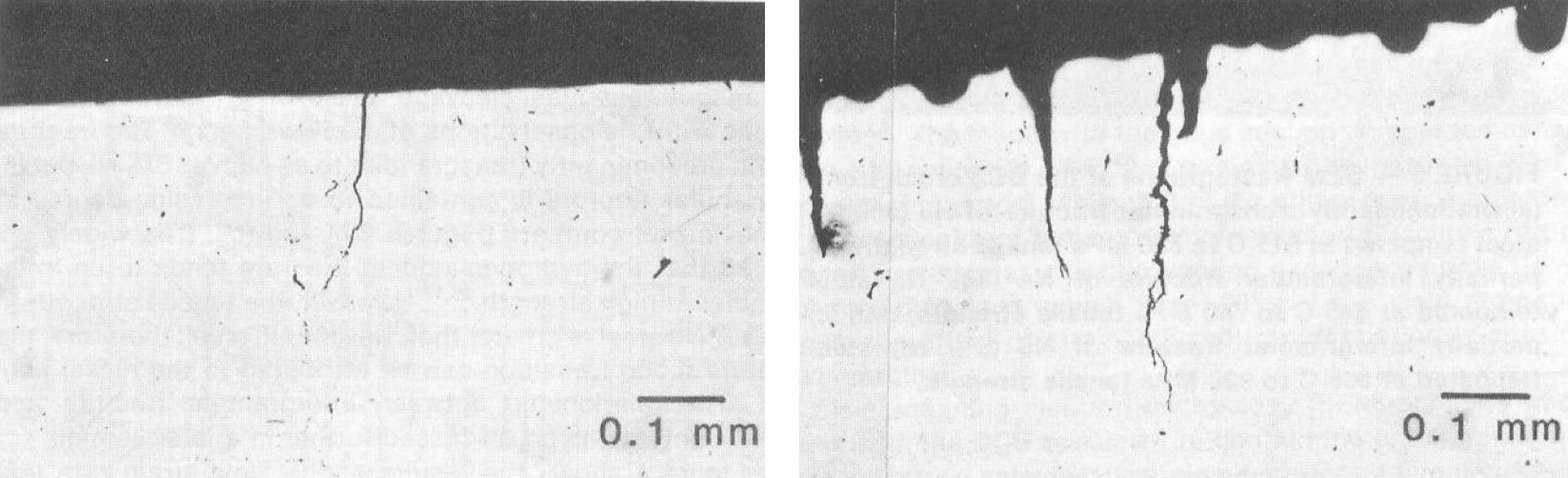
In the subsea oil and gas industry, cracking of duplex and super duplex stainless steels (DSS and SDSS, respectively) is a common example of HSC due to hydrogen generated by cathodic protection [14]–[15]. In this regard, subsea equipment is protected against external corrosion by sacrificial Al-Zn-In anodes, where indium is used to prevent passivation. Subsea components are, therefore, cathodically polarized to about –1.05 \(V_{{Ag/AgCl}_{\text{seawater}}}\). At this potential, the HRR is the dominant cathodic reaction, Figure 1. Subsea failures of DSS and SDSS components had led to significant research and the development of an industry recommended practice [16].
Preventing EAC in oil and gas production.
It is well known that EAC requires the exposure of a susceptible material or microstructure to an aggressive environment stressed above a certain critical value. The need for the concurrent action of these three variables is commonly represented using a Venn Diagram, Figure 3. In many instances, the environment that will lead to hydrogen evolution or localized corrosion is: i) not easy to predict, and/or ii) it is fixed, as in the case of hydrogen generated by cathodic protection. Therefore, design codes address the two factors that can be controlled by engineers, namely the material and the utilization, i.e., allowable design stresses, of the component.
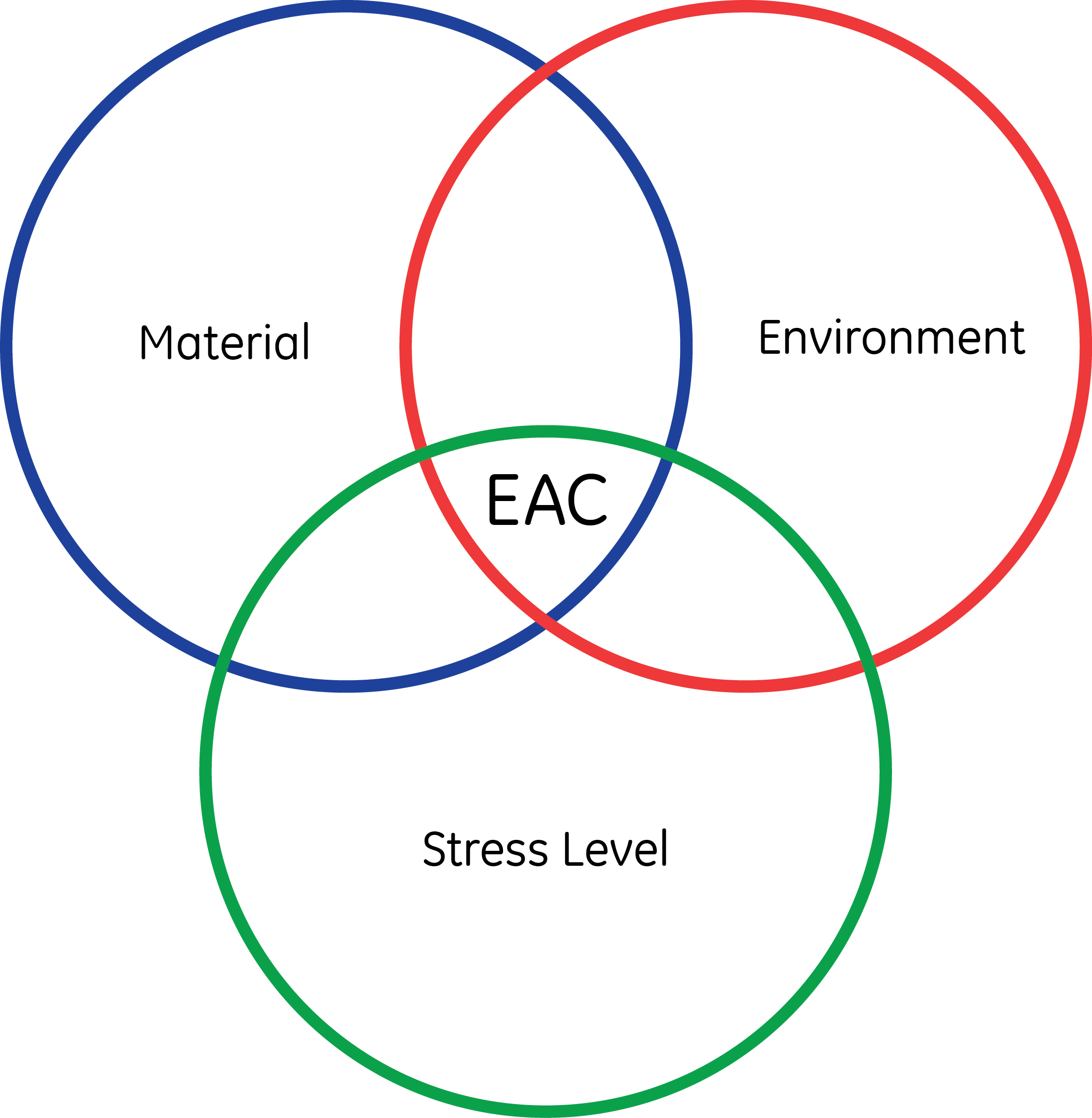
Materials selection for oil and gas production in sour environments is governed by the ISO 15156 standard. Part No. 2 of ISO 15156 covers carbon and LAS and Part No. 3 deals with CRA [2], [17]. The philosophy behind ISO 15156–2 is to control the material’s strength, hardness, and cleanliness. In the oil and gas industry, carbon and LAS are all selected to comply with Region 3 (i.e. severe sour service). Carbon and LAS are, thus, restricted to a maximum hardness of 250HV for the base metal and 275HV for weld caps as weld caps are not in direct contact with production fluids. No subsea field to date has challenged those restrictions or qualified materials for, e.g., Region 2 – intermediate sour service. Additionally, ISO 15156–2 limits the use of nickel as alloying element in LAS to 1.0 wt%. We think the nickel limit is unjustified [18]. You can read more about the history of ISO 15156/NACE MR0175 and the 1wt% limit here and here.
In oil and gas production the aggressive sour environment cannot be prevented, and corrosion inhibition is not always effective for complex equipment such as valves, tress, blowout preventers, and manifolds. Therefore, imposing a maximum on hardness, strength, and cleanliness addresses the other two factors: the material and the maximum stress.
In contrast to Part No. 2, ISO 15156–3 sets strict environmental boundaries in addition to strength and hardness limits. Environmental limits include temperature, pH, \(P_{H_2S}\), chloride concentration, and \(S^0\). The standard is divided into sections based on alloy family. Each family has a series of tables describing current acceptance criteria for a particular set of alloys. Companies can help refine the limits and add new alloys through a balloting process.
Finally, DNV-GL in partnership with several oil and gas operators, materials suppliers, and original equipment manufacturers, has developed DNV-RP- F112, a recommended industry practice that regulates the use of DSS and SDSS exposed to cathodic protection [16]. Recognizing that subsea components made of DSS and SDSS will be inevitably exposed to hydrogen (Figure 1), the standard defines a maximum austenite spacing and a maximum allowable design stress. In this regard, fine austenite spacing decreases the alloy’s susceptibility to HSC (referred to as Hydrogen Induced Stress Cracking, HISC, by DNV) since austenite grains help arrest cracks initiated in the ferrite phase [14]–[15].
Summary
The answer to the initial question is “no, pits are not always a prerequisite for environmentally assisted cracking”. Whereas anodic processes such as SCC typically initiate from pits, HSC occurs in the absence of localized corrosion. Sharp threads and notches serve as stress concentration sites that lead to HSC initiation.
But if SSC is a cathodic process, why do we see cracking originating from elongated pits and trenches? The answer will be in the next post!
References
- ASTM NACE/ASTMG193–12d, “Standard Terminology and Acronyms Relating to Corrosion”, ASTM International, West Conshohocken, PA, 2012.
- ISO 15156–2, “Petroleum and natural gas industries — Materials for use in H2S-containing environments in oil and gas production. Part 2: Cracking-resistant carbon and low-alloy steels, and the use of cast irons.,” International Organization for Standardization (ISO), Geneva, Switzerland, (2015).
- Yamane, Y. et al., Paper No. 167: “Effect of Ni on sulfide stress corrosion cracking in low alloy steels.” Corrosion/86, (NACE International, Houston, TX, March, 1986).
- “Pushing the limits of metals in corrosive oil and gas well environments.” Corrosion 63, 63–100 (2007). Rhodes, P.R., Skogsberg, L.A. & Tuttle, R.N.
- “Environment-assisted cracking of corrosion-resistant alloys in oil and gas production environments: a review.” Corrosion 57, 923–966 (2001). Rhodes, P. R.
- “Hydrogen Embrittlement of Metals Atomic hydrogen from a variety of sources reduces the ductility of many metals.” Science 159, 1057–1064 (1968). Rogers, H. C.
- “Hydrogen Damage and Embrittlement”, in ASM Handbook, Volume 11: Failure Analysis and Prevention (eds Becker, W. T. & Shipley, R. J.) 809–822 (ASM International, Metals Park, OH, 2002). Buy at Amazon. Kim, C. D.,
- “Hydrogen embrittlement of steels.” Annual review of materials science 8, 327–357 (1978). Oriani, R. A.
- “Whitney Award Lecture–1987: Hydrogen-The Versatile Embrittler.” Corrosion 43, 390–397 (1987). Oriani, R. A.
- “Sulfide stress cracking resistance of low-alloy nickel steels.” Corrosion 42, 222–233 (1986). Yoshino, Y. & Minozaki, Y.
- “Laboratory Testing of Metals for Resistance to Sulfide Stress Cracking and Stress Corrosion Cracking in \\(H_2S\\) Environments,” NACE International, Houston, TX, (2005). TM–0177,
- “The formation of ferrous monosulfide polymorphs during the corrosion of iron by aqueous hydrogen sulfide at 21°C.” Journal of the Electrochemical Society 127, 1007–1015 (1980). Shoesmith, D. W., Taylor, P., Bailey, M. G. & Owen, D. G.
- “Electrochemical Model of Mild Steel Corrosion in a Mixed \\(H_2S\\)/\\(CO_2\\) Aqueous Environment in the Absence of Protective Corrosion Product Layers.” Corrosion 71, 316–325 (2015). Zheng, Y., Ning, J., Brown, B. & Neic, S.
- “Effects of cathodic protection on duplex stainless steels in seawater.” Corrosion 53, 234–240 (1997). Francis, R., Byrne, G. & Warburton, G. R.
- “Resistance Toward Hydrogen-Induced Stress Cracking of Hot Isostatically Pressed Duplex Stainless Steels Under Cathodic Protection.” Corrosion 66, 115004–115004 (2010). Lauvstad, G. Ø., Johnsen, R., Asbjørnsen, I., Bjurstro m, M. & Hjorth, C.-G.
- “Design Of Duplex Stainless Steel Subsea Equipment Exposed To Cathodic Protection,” Det Norske Veritas (DNV-GL), Høvik, Norway, (2008). DNV-RP-F112,
- “Petroleum and natural gas industries — Materials for use in H2S-containing environments in oil and gas production. Part 3: Cracking-resistant CRAs (corrosion-resistant alloys) and other alloys.” International Organization for Standardization (ISO), Geneva, Switzerland, (2015). ISO 15156–3,
- “Sulfide stress cracking of nickel-containing low-alloy steels.” Corrosion Reviews 32, (2014). Kappes, M., Iannuzzi, M., Rebak, R. B. & Carranza, R. M.