The presence of carbon dioxide increases the corrosion rate of carbon and low alloy steels (LAS) by accelerating cathodic reaction kinetics (1-8). In aqueous solutions, dissolved carbon dioxide hydrates to form carbonic acid according to (1-5):
$$C{O_2} + {H_2}O \leftrightarrow {H_2}C{O_3} \label{a} \tag{1}$$where KHyd is the equilibrium constant for the CO2 hydration reaction, approximately 10-3 at 25°C (1).
Carbonic acid dissociates to bicarbonate, \({\rm{HCO}}_3^ -\), while bicarbonate further dissociates to carbonate \({\rm{CO}}_3^{2 – }\) (1-4). It is now agreed that, for temperatures below 50-60°C, hydration of carbon dioxide to carbonic acid is the rate-controlling step (1-4), i.e., the slowest process. Figure 1 shows the speciation diagram of carbon dioxide in a 1-wt% NaCl solution with a partial pressure of CO2 (pCO2) of 1 bar at 25°C (1). Given that, at a given temperature, the concentration of dissolved CO2 is constant and related to the pCO2 by Henry’s law, the concentration of H2CO3 is independent of solution pH and proportional to the hydration constant KHyd (1). In contrast, bicarbonate and carbonate concentrations are a function of pH. For the conditions shown in Figure 1, bicarbonate becomes the predominant species at a pH above 3.70, whereas carbonate-carbonic acid equivalence point is approximately pH 7.0 (1).
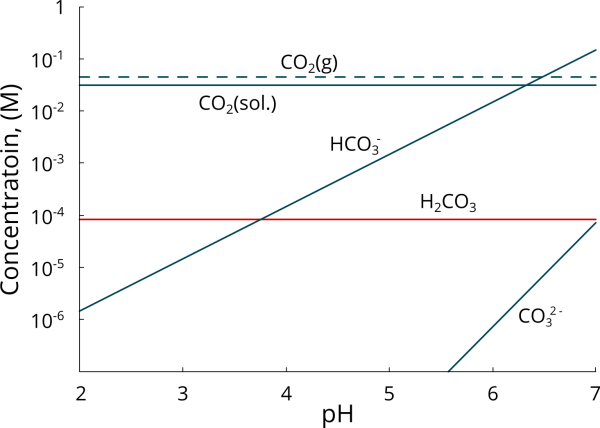
Cathodic reactions
The presence of CO2 accelerates the corrosion process by increasing the rate of the hydrogen evolution reaction (1-5). Although the actual mechanism is not fully understood, most researchers agree on that, like most weak acids, carbonic acid produced by the hydration of dissolved CO2 can be reduced to hydrogen directly without dissociating into protons (H+) (1-8). Thus, at a given pH, the presence of CO2 leads to a much higher corrosion rate than would be found in a strong acid of the same pH (1-4). The two main cathodic reactions at pH < 5.0 are (1-4):
At pH = 5.0, the direct reduction of water molecules is possible (1-4):
Gray et al. (9) proposed that at elevated pHs, bicarbonate can be reduced to hydrogen gas according to:
Nešić argues that Equation 5 is hard to distinguish experimentally from Equations 2 and 3, pointing out that, while \({\rm{HCO}}_3^ -\) concentration steadily increases in the 3.50 < pH < 7.0 range, corrosion rates decrease with pH in the same pH range (3-4). However, the reduction in corrosion rate at the open circuit potential could be associated with the formation of a protective iron carbonate film (or other form of protective scale) and does not invalidate the reaction path proposed by Gray and coworkers. Moreover, bicarbonate concentrations increase logarithmically rather than steadily as suggested by Nešić. At a pCO2 of 1 bar, bicarbonate concentrations become predominant at pH > 3.70, with a concentration that is almost 2 orders of magnitude higher than carbonic acid at pH 6.0 and almost 4 orders of magnitude higher at pH 7.0, i.e. the typical pH range of formation water, Figure 1. Regardless of the reaction path, Equations 2 to 5 are all equivalent.
Finally, in the presence of organic acids, such as acetic acid (CH3COOH) and hydrogen sulfide (H2S), the other two possible cathodic reduction reactions are (2):
Anodic reactions
In its simplest form, the main anodic reaction is the dissolution of iron to ferrous ions:
This reaction has been found to have a strong pH dependence for pH < 4.0 (10). In strong acids, Bockris et al. proposed the following reaction path, which is valid for pH < 4.0 (10):
In the Bockris-Drazic-Despic (BDD) mechanism, the oxidation of Fe+1 to Fe+2 is the rate-determining step (RDS). The BDD mechanism predicts a Tafel slope of 40 mV per decade at 25°C. Above pH 4.0, the anodic reaction can be considered pH-independent for the typical pH range of most produced water environments (1-4). The actual reaction path and rate-controlling steps are, however, not well understood. The work by Nešić (1, 3-4) and Dugstad (2) can be consulted for more information on this topic.
References
- S. Nešić, “Carbon Dioxide Corrosion Of Mild Steel”, in Uhlig’s Corrosion Handbook, Third Edition, Edited by R. Winston Revie (John Wiley & Sons, New York, 2011): p.229-245. Buy at Amazon
.
- A. Dugstad, “Fundamental aspects of CO2 metal loss corrosion part I: mechanism”, CORROSION/06, Paper no 611, (NACE International, Houston, TX, 2006).
- S. Nešić, J. Postlehwaite, and M. Vrhovac, “CO2 corrosion of carbon steel – from mechanistic to empirical modeling”, Corrosion Reviews 15 (1-2), (1997):p.211-240.
- S. Nešić, “Key issues related to modeling of internal corrosion of oil and gas pipelines – A review”, Corrosion Science 49, (2007): p.4308–4338.
- M.B. Kermani and A. Morshed, “Carbon Dioxide Corrosion in Oil and Gas Production — A Compendium”, Corrosion 59, (2003): p.659-683.
- C. de Waard, D.E. Milliams, “Prediction of carbonic acid corrosion in natural gas pipelines”, Proceedings 1st International Conference on the Internal and External Protection of Pipes, Paper F1, (BHRA Fluid Engineering, University of Durham, Durham, United Kingdom, September 9-11, 1975).
- C. de Waard, U. Lotz, and D.E. Milliams, “Predictive model for co2 corrosion engineering in wet natural gas pipelines”, Corrosion 47, (1991): p 976-985.
- C. de Waard, D.E. Milliams, “Carbonic acid corrosion of steel”, Corrosion 31, (1975): p.177-181.
- Gray, L.G.S., Anderson, B.G., Danysh, M.J. and Tremaine, P.G., “Mechanism of carbon steel corrosion in brines containing dissolved carbon dioxide at pH 4”, Paper No. 464 in: Corrosion/89, Houston, TX: NACE International, 1989
- J.O.M. Bockris, D. Drazic, A.R. Despic, “The electrode kinetics of the deposition and dissolution of iron”, Electrochim. Acta 4, (1961): p.325.
Update
- 16 January 2020: fixed typos and updated LaTex code to meet the newest MathJax requirements.